Cet article plus technique est destiné à ceux qui sont déjà familiarisés avec la chimie des émaux et avec les progressions silice/alumine.
Le “nombre d’or” d’un émail stable : rapport .3/.7 entre R2O et RO
La Formule de Seger – ou “formule Unité” ou encore “UMF” pour “Unity Molecular Formula” donne la liste des oxydes qui composent un émail. Connaître ces oxydes permet d’ensuite composer l’émail avec “nos” matières premières. Mais c’est aussi un langage universel qui nous permet de prédire son comportement.
Premier point à noter : les émaux les plus stables ont un rapport de 0.3 mole de NaKO pour 0.7 moles de CaO. Sur cette base, en 1912 déjà, Stull a établi son diagramme. Cet outil permet de prévoir quels émaux vont tressailler, être incuits ou sous-cuits, mats, satinés ou brillants en fonction de la proportion d’alumine et de silice. Stull travaillait au cone 11.
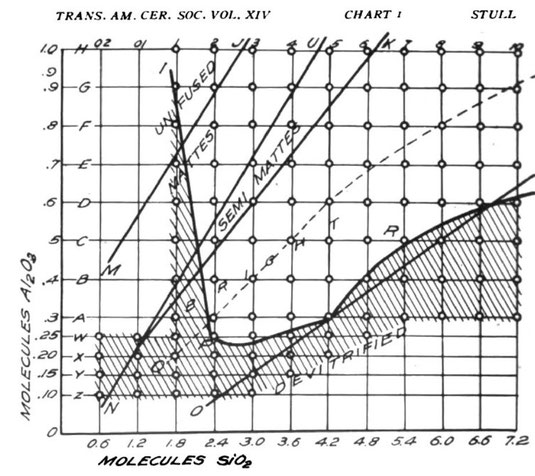
Et ce diagramme a été réalisé pour 0.3 alcalis et 0.7 alcalino-terreux.
La zone hachurée correspond au tressaillage.
Dans le coin supérieur gauche (silice basse et alumine haute) ainsi que dans le coin inférieur droit (silice haute et alumine basse) : la fusion n’est pas complète – c’est ce qu’on appelle des émaux « immatures ». Voir aussi la remarque plus bas dans ce texte, qui distingue la zone “unfused” et “devitrified”, parce que ce ne sont pas les mêmes phénomènes.
Bien sûr s’il y a simultanément silice haute et alumine haute, l’émail ne va pas fondre non plus – par insuffisance de fondants.

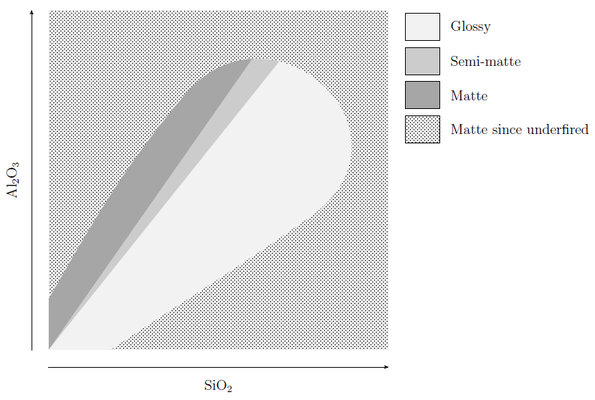
Source images : Mostert P., Understanding the Stull Chart, Glazy Help – Ceramics Wiki.
La zone “Mature” est divisée en trois : mats, semi-mats et brillants. La frontière entre mat et semi-mat compte environ 4 moles de silice pour 1 d’alumine. La frontière entre semi-mat et brillant a environ 5 moles de silice pour 1 d’alumine.
Autrement dit
si le ratio silice/alumine < 4 : on aura des mats
si le ratio silice/alumine > 5 : on aura des brillants
et entre les deux on obtiendra du semi-mat.
Sur la ligne du ratio 7.5 silice pour 1 alumine on aura la zone centrale des brillants.
Limites des outils prédictifs
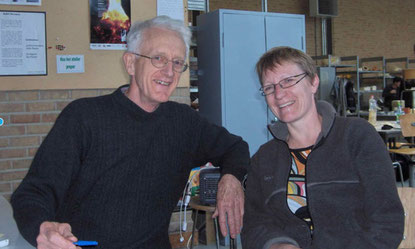
Bien sûr ce graphique ne peut pas donner avec certitude le comportement d’un émail, il peut y avoir des exceptions :
- la nature du tesson,
- l’épaisseur de la pose,
- les autres oxydes présents,
- la vitesse de refroidissement…
Ces facteurs jouent énormément, mais ce schéma donne une idée générale. Par exemple pour matifier un émail brillant on peut tenter de diminuer le ratio silice/alumine. S’il y a beaucoup de silice dans la recette de base, il suffira peut-être de diminuer un peu la silice, ce qui sera simple à faire.
Du cône 10-11 au cône 6-7
Cependant la température cone 11 est fort élevée. Actuellement nous sommes nombreux à vouloir cuire autour du cone 6, parce que pour la plupart nous utilisons des fours électriques. Cuire à cone 6 diminue fortement la facture d’électricité et use moins vite les fours. De plus, depuis une vingtaine d’années, de nombreux céramistes ont contribué à développer des émaux attrayants à cette température plus basse.
Pour baisser la température on peut ajouter un peu de Bore : Matt Katz a étudié la proportion idéale à ajouter, en moles bien sûr, en fonction de la température de cuisson. Il a ensuite communiqué ses résultats lors du NCECA en 2012. Concrètement pour le problème qui nous occupe, ajouter 0,15 mole de Bore permet de passer de cone 11 à cone 6.
En se basant sur la recherche de Matt Katz (qui je crois a été son professeur), SueMcLeod a voulu voir si le diagramme de Stull restait valable à cone 6, avec ce fameux ajout de 0,15 mole de Bore. Elle a communiqué ses résultats au NCECA en 2018, sur base d’une série d’échantillons et miracle : ça marche ! La présentation complète de ses résultats (en anglais) peut être trouvée ici : https://suemcleodceramics.com/understanding-cone-6-nceca-presentation-2018/. Elle a utilisé comme Stull : 0.3 NaKO pour 0.7 CaO mais en ajoutant 0.15 B2O3.
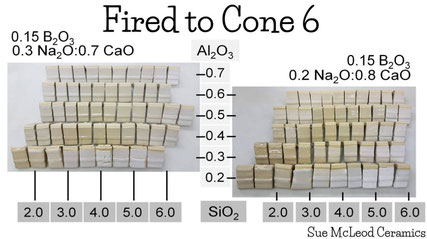
Lorsqu’on observe de près les échantillons de SueMcLeod (voir la photo dans l’article en lien), les zones “devitrified” et “unfused” sont très différentes. La zone “devitrified” contient beaucoup de silice : elle a été fondue mais a un retirement, il semble que la silice en fusion a une tendance à se rassembler sur elle-même (c’est une question de tension superficielle). La zone “unfused” a tellement d’alumine (encore plus réfractaire que la silice) que c’est impossible à fondre.
Si vous voulez vérifier par vous-mêmes, j’ai calculé une recette qui peut être un bon point de départ pour une progression silice-alumine quasi identique : Néphéline syénite 65%, fritte boro-calcique M9152 10% et craie 25% – ce qui correspond au point de départ suivant, exprimé en formule de Seger :
NaKO 0,3 Al203 0,34 SiO2 1,41
CaO 0,7 B2O3 0,15
Les valeurs d’alumine et silice sont très basses car cette recette correspond donc au coin inférieur gauche d’une progression dans laquelle on va incrémenter la silice et/ou l’alumine. J’ai l’habitude de réaliser les progressions Si/Al selon la méthode de Ian Currie, qu’il a présentée dans son livre Revealing glazes Using the grid method (complété par Stoneware glazes, a systematic approach). Vous trouverez un descriptif de sa méthode en anglais ici. Mais il existe d’autres façons de réaliser des progressions silice-alumine : voyez le site glazy.org, ou encore la méthode d’Alain Fichot (qu’il a appelée « Ernest ») – ici un lien vers le PDF où il l’explique en la comparant avec celle de Glazy.
A vous de voir celle qui vous convient le mieux, l’important étant de comprendre ce que l’on fait afin de pouvoir tirer des enseignements et conclusions pour les émaux et glaçures que nous choisirons d’utiliser.
Une réponse sur « Formule de Seger et Diagramme de Stull : un article expert »
Merci Joëlle pour cette “piqûre de rappel”, bienvenue pour rafraîchir nos connaissances en chimie et en composition des émaux. Il me semble important, voire nécessaire de comprendre ce que l’on fait quand on manipule les produits qui composent les émaux dont on recouvre nos pièces utilitaires. Céramicalement